Průvodce odlehčováním pro moderní strojaře Autodesk
Kdo se nikdy nesnažil odlehčovat, jako by nebyl – nižší hmotnost totiž prospěje libovolnému produktu.
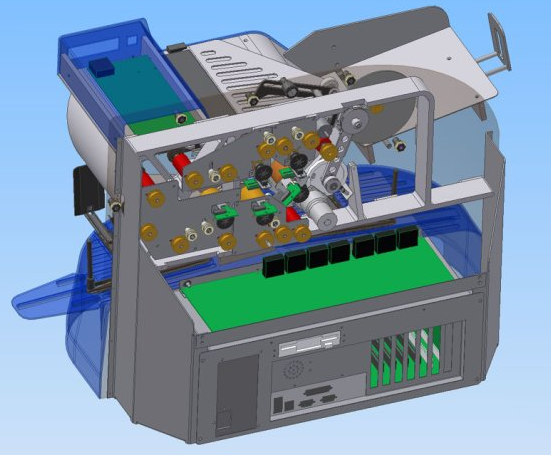
Odlehčete je a potěšíte zákazníky nižší spotřebou paliva. Navrhujete spotřební zboží? Pak nejspíš dobře víte, jakou roli hraje u zákazníků při výběru ze dvou podobných výrobků právě hmotnost. Také u průmyslových strojů se odlehčení vyplácí – přispívá totiž ke snížení spotřeby energie a zrychlení provozu.
Háček je v tom, že odlehčování je jen jedním z cílů, kterých se vývojáři i konstruktéři snaží dosahovat, a těm ostatním zdatně konkuruje. Jak přijít s produktem, který splní všechna vymezená kritéria, bude co nejlevnější a zároveň co nejlehčí?
Pojďme se nejdřív ze všeho podívat na to, proč je dnes odlehčování „in“ a proč o něj tolik vývojářů a konstruktérů usiluje.
Odlehčit je potřeba všechno, co se hýbe. To se samozřejmě týká letadel, vlaků nebo například aut. Tím to ale nekončí, tuto zásadu můžeme aplikovat i na pohyblivé součásti průmyslových strojů nebo na spotřební zboží, které lidé nosí u sebe. Pohyb totiž vyžaduje energii – a čím je libovolná věc lehčí, tím méně energie potřebujete k tomu, abyste ji rozpohybovali. V konečném součtu vůbec nezáleží na tom, jestli má tuto energii vyvinout váš zákazník sám, nebo to za něj udělá motor. Lehčí produkt budou zákazníci zkrátka vnímat lépe.
Bionická přepážka v letadlech Airbus. Nový model přepážky je o 30 kg (celých 45 %) lehčí než přepážky předchozí. Společnost Airbus odhaduje, že jí každá odlehčená přepážka ušetří až 3,2 tuny paliva za rok. Zdroj fotografie: Airbus.
U letadel každý ušetřený kilogram hmotnosti sníží roční spotřebu paliva o 106 kg. U aut zase může 10% odlehčení zvýšit palivovou účinnost až o 3 %.1 Ve světě existují dokonce i normy, které každoroční zvyšování palivové účinnosti u osobních i nákladních vozidel přímo vyžadují, např. americké emisní standardy CAFE.
Odlehčení se promítá i do dalších oblastí. Odlehčete součástky poháněné motory a zkrátíte délku cyklu, případně zvýšíte kapacitu, a přímo tím ovlivníte ziskovost provozu. Lehčí auta mají vyšší maximální nosnost, najedou více kilometrů, snáze se ovládají, lépe zrychlují a déle vydrží. U větrných turbín se v současnosti používají uhlíková či skleněná vlákna, díky nimž lze prodloužit listy rotoru a používat turbíny i při vyšších rychlostech. Takové odlehčení o 20–30 % může množství vygenerované energie až ztrojnásobit.
U spotřebního zboží, například elektroniky nebo kufrů a batohů, bývá odlehčený produkt ergonomičtější a lépe se chová. Cyklistům přináší lehčí vybavení rychlejší jízdu a lepší prožitek, mnoho sportovně založených spotřebitelů zase ocení, že odlehčené chrániče a helma tolik nepřekáží.
Zároveň je nutné zmínit, že při vhodném odlehčení se na produkt spotřebuje méně materiálu, což může dokonce snížit výrobní náklady. Neplatí to ale vždycky – když například těžký, levný materiál vyměníte za lehčí, který je nákladnější obstarat nebo vyrobit, může se výrobek naopak prodražit.
Odlehčením můžete ušetřit i na dopravě, na druhou stranu je třeba vzít v potaz, že se výpočet ceny za přepravu v poslední době změnil a částka se neodvíjí jen od hmotnosti. Přední přepravci (UPS, DHL a další) už dnes přepravu účtují podle objemové hmotnosti. Ta se vypočítává mimo jiné i podle rozměrů balíku. Při snižování nákladů na přepravu si tak nevystačíte jen s odlehčováním, ale musíte také minimalizovat rozměry zabaleného zboží.
Při odlehčování vždy hledáte kompromis. Nemůžete totiž z výrobku odstranit hmotu bez toho, aby to ovlivnilo jeho vlastnosti. Dobrou zprávou ale je, že je významná část produktů kvůli bezpečnosti „naddimenzovaná“ a že požadavky na pevnost splníte, i když produkty na vhodných místech odlehčíte. Na druhou stranu byste měli vzít v potaz i další faktory, které možná nejsou tolik zjevné.
Když zvažujete, jaké bude mít odlehčení produktu dopady, je na prvním místě vždy bezpečnost. Například v automobilovém průmyslu jsou bezpečnostní opatření nejdůležitějším faktorem, který stojí za nárůstem hmotnosti vozidel. Kvůli zajištění bezpečnosti byl průměrný americký vůz v roce 2008 o 240 kg (tedy 20 %) těžší než auta, která se po USA proháněla před 20 lety.3 V posledních letech sice hmotnost vozů růst přestala, ale bezpečností jsme při odlehčování omezeni i nadále.
Lehčí díly jsou náchylnější k poškození vibracemi, proto musíte svědomitě vyhodnotit, při jaké frekvenci u nich dochází k rezonanci – a zabránit tak tomu, aby fatálně selhaly v provozu. Hrozí také, že budete muset přidat tlumení – a že z odlehčení nakonec nic nebude.
Chcete použitý materiál nahradit lehčím? Pak vás nezajímá jen jejich hustota. Od prostředí, ve kterém se produkt bude používat, se odvíjejí i požadavky na teplotu, tlak, vodivost nebo například odolnost vůči působení chemických látek.
Lehčí díly můžou být i dražší. To platí obzvlášť tehdy, když při výměně materiálu vsadíte na uhlíkové vlákno nebo jiné kompozitní materiály. Nadto v takovém případě potřebujete získat nové dovednosti, abyste se s materiálem naučili zacházet. Pokud ještě k tomu přijdete s komplexnější geometrií, strávíte s vývojem odlehčeného produktu více času a celý proces bude složitější. I když se rozhodnete komplikacím vyhnout a raději „jen“ vyrábět stávající produkty modernější metodou, počítejte s tím, že vám zabere poměrně dost času díly přepracovat a někdy i konsolidovat.
Další náklady jdou na vrub novějším výrobním procesům: křehčí díly bude potřeba zpevnit a přilepit, a výroba je rázem složitější a náročnější na zdroje.
Při odlehčování nesmíte zapomínat ani to, jak celou věc vnímají zákazníci – a co od vás očekávají. V některých případech platí, že v zákaznících lehčí produkt nevyvolává důvěru, působí na ně totiž levně a nekvalitně. Takový dojem můžete v zákaznících například vyvolat, když na první pohled odolné díly z kovu nebo hliníku nahradíte plastem. Stojí tedy za to při navrhování produktu zvážit, jak budou zákazníci vnímat plastové části, které se snaží napodobit materiály přírodní – a podle toho se rozhodnout, zda je zvolit, či ne.
Nesmíme zapomenou zmínit ani dominový efekt, který se odlehčováním často spustí. Jak to vypadá v praxi? Jedna věc je nahradit těžší materiál lehčím (například u autodílu přejít od oceli k hliníku), druhá věc je si poradit s navazujícími kroky, které změna přinese. Vezměme si třeba lakování: jinak budete lakovat plech a jinak uhlíkové vlákno. To je navíc poréznější a jeho povrch je narozdíl od plechu hrbolatý a nerovnoměrný.
Dominový efekt se projeví například i tehdy, když vyměníte materiál, který v procesu výroby sváříte. Svařování hliníku (nebo jeho přivařování k oceli) vám možná ušetří čas a produkt odlehčí, protože jsou sváry lehčí než nýty, na druhou stranu tento technologický postup ještě není zaužívaný, je energeticky náročnější a zatím se používá jen v malosériové výrobě.4
Jak je vidět, musíte si při odlehčování poradit s mnohými výzvami – a proto je nasnadě si ušetřit práci tím, že použijete některý z osvědčených přístupů. Dobře si promyslete, který z nich zvolíte, každý se totiž nejlépe hodí pro jinou situaci a je klíčové vybrat ten správný.
Nejčastěji se odlehčuje tak, že nahradíte stávající materiál jiným s nižší hustotou. Díky pokroku ve výrobě polymerů, kovů a kompozitů máme dnes k dispozici lehčí a odolnější materiály, které jsou zároveň levnější než kdy dřív.
Často i tak na plné čáře vítězí ocel, má totiž rozumný poměr pevnosti k hmotnosti. Přesto se díky novým slitinám i výrobním technologiím stále častěji uplatňují i lehčí materiály. Takový hliník například váží o dvě třetiny méně než ocel a je na naší planetě nejrozšířenějším kovem. Na oblíbenosti získává i hořčík, který je lehký, pevný, tuhý, rozměrově stabilní a dobře odolává nárazům, vibracím i deformacím. Ne nadarmo jde o nejlehčí kov, který se dnes používá v konstrukcích.
Slitiny hořčíku se čím dál více uplatňují u výrobků a nástrojů, které zákazník přenáší – najdeme je v mobilních telefonech, noteboocích, jízdních kolech nebo třeba v žebřících, motorových pilách a výtazích. Své místo si vybojoval i v leteckém a automobilovém průmyslu: u aut se používá například v sedadlech, konzolích motorů a pedálů nebo v rozvodovkách.
Vhodnou alternativou k dílům z kovu může být v některých případech plast nebo kompozitní materiál, jako karbonové, skleněné nebo kevlarové vlákno. Všechny tři zmíněné kompozity jsou přibližně stejně pevné, kevlar a karbonové vlákno ale mají výrazně lepší poměr pevnosti k hmotnosti. Existují i další, novější materiály, které jsou tepelnou a chemickou odolností dost podobné kovům – a i ony se postupně začínají ve výrobě využívat.
Při odlehčování ale nehraje roli jen materiál, ale i výrobní metody. Ještě donedávna jsme byli ostatně výrazně limitováni tradiční subtraktivní výrobou, což byl problém zejména u kovových dílů a součástek. Pokroky v oblasti aditivní výroby nám ale postupem času příjemně uvolnily ruce.
Vůbec poprvé v historii si například můžete pohrát s vnitřní strukturou dílu. Když na 3D tiskárně vyrobíte díl se strukturou včelí plástve, zachováte jeho pevnost a snížíte množství použitého materiálu v porovnání s obráběním nebo odléváním.
Podobné výsledky vám přinese mikrobuněčné vstřikování – tedy vstřikování se sycením plynem. Při něm se do taveniny polymeru vpraví plyn a celá směs se vstříkne do formy, čímž v tavenině poklesne tlak (asi jako když otevřete lahev minerálky). Vzniknou tak bublinky plynu, které taveninu napění, a výsledný materiál je o 20–40 % lehčí.
Další možností je konsolidace dílů – tam, kde je to možné, se kovové části nahradí plastovými, které se pak snáze spojují do jednoho dílu, např. pomocí 3D tisku. U kovů se dá obrábění nebo lisování nahradit tenkostěnným odléváním, což lze využít především u hořčíku. Hotové díly jsou lehčí a zachová se integrita konstrukce
Hmotnost konstrukcím přidávají i šroubové, maticové a nýtové spoje. Pracuje se tak na tom, abychom dovedli svařovat i materiály, u kterých to bylo donedávna nemožné. General Motors nebo Tesla se například soustředí na svařování hliníku, případně hliníku s ocelí. Nové adhezivní technologie nám dovolují slepovat i materiály, u kterých to bývalo nemyslitelné – a umíme si poradit i s vyšší hmotností, rozdílností materiálů, vibracemi a teplotou.
V neposlední řadě nesmíme zapomenout na technologie, které vám poradí, kde výrobek odlehčit. Už v úvodních fázích vývoje můžete nástroji pro simulaci provést pevnostní a bezpečnostní analýzu a na jejím základě přicházet s dalšími verzemi modelu. Moderní software pro konstruktéry už dnes obsahuje i nástroje pro topologickou optimalizaci. S jejich pomocí zjistíte, které části dílu nejméně přispívají k jeho tuhosti a pevnosti a můžete je s čistým svědomím odstranit.
To ovšem zdaleka není všechno. Objevují se nové, pokročilejší materiály a technologie, jako jsou uhlíkové nanočástice, 3D tisk z kombinací materiálů a generativní design. Budoucnost odlehčování je tak více než slibná. Například uhlíkové nanočástice (známé i jako uhlíkové nanotrubice nebo CNT) mají pevnost v tahu 33x vyšší než kevlar. Zatím jsou sice ve stádiu výzkumu, ale vkládá se do nich mnoho nadějí. 3D tisk z kombinací materiálů zase bude nepochybně aditivní technologií příští generace – budeme totiž před výrobou samotného dílu umět vyrobit materiál s požadovanými vlastnostmi. Generativní navrhování nám pak umožní zkombinovat CAD, CAE a CAM a jejich iterativní povahu v jednom uceleném procesu: konstruktéři zkrátka jen zadají parametry a obratem získají ideální díl správné velikosti.
Není pochyb o tom, že výrobu díky těmto pokrokům čeká zářná budoucnost. Nemusíme ale nečinně sedět a vyčkávat. Už dnes totiž máme na výběr z téměř nekonečné nabídky možností a metod, které nám s odlehčováním pomohou. Moderní materiály a výrobní metody nám umožňují vyrábět tvary, které donedávna vypadaly jako ze sci-fi filmů, umíme si pohrát s vnitřní strukturou dílů a pokročilé CAD, CAE a CAM technologie vedou k výrobě produktů, které jsou levnější, pevnější, lehčí – zkrátka a jednoduše lepší než kdy dřív.
Zdroje:
- Forbes, „How to Build a Car that Gets 54.5 MPG“, https://www.forbes.com/pictures/ehmk45lii/weight-reduction/
- Composites World, „Wind turbine blades: Glass vs. carbon fiber“, https://www.compositesworld.com/articles/wind-turbine-blades-glass-vs-carbon-fiber, 31. května 2012
- EPA report, Light-Duty Automotive Technology, Carbon Dioxide Emissions, and Fuel Economy Trends: 1975 Through 2015
- Automotive News, „GM’s learning curve on lightweighting“, https://www.autonews.com/article/20151110/BLOG06/311119999/gms-learning-curve-on-lightweighting, 10. listopadu 2015